Working with Burl: When Beautiful Meets Complex
At Flexhouse, we’re no strangers to bold design challenges. Recently, we had the opportunity to take on a project for a renowned global brand involving one of the most intriguing materials in woodworking: Burl veneer, specifically Burl Oak and Burl Walnut (American Black Walnut).
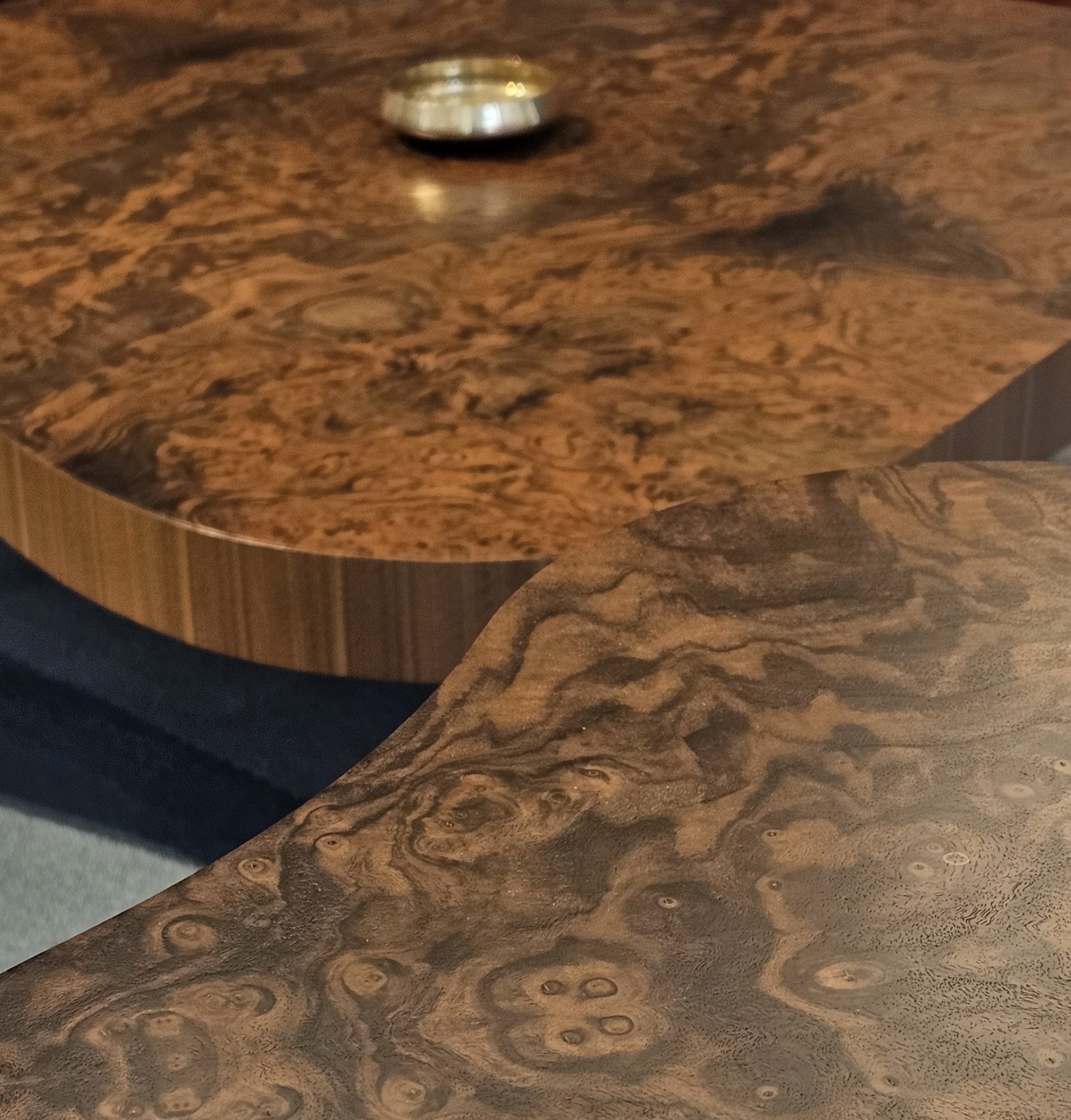
At first, we were drawn in by the richness of the design and the learning opportunities. But as the project progressed, we quickly realized how many production challenges this beautiful but temperamental material would bring.
Rare, Raw & Unforgiving: The Nature of Burl
Burl veneer is known for its intensely figured grain, which creates a visual depth that can’t be replicated by straight-grain woods. But beauty comes at a cost: to cover just 1 square meter of a coffee table surface, we needed to join up to eight separate veneer leaves—each with a unique pattern.
Finding high-quality Burl veneer is another task in itself. It's rare, often comes in short or narrow sheets, and many leaves contain cracks, voids, or wormholes. To tackle this, we developed a custom wax filler technique to seal and stabilize the material before beginning the finishing process.
From Handwork to Innovation: The 65 mm Challenge
The design called for a tabletop 65 mm thick, a rarity in veneer-based production. No machine on the market could apply edge-banding at that thickness, so we initially handled it by hand. While possible, it was slow and lacked precision.
We eventually partnered with a Danish manufacturer to develop a custom edge bending machine capable of working at 65 mm. This brought precision and speed—but also revealed a new problem. The larger version of the table became so heavy that four people were needed to lift it off the lacquer line—a logistical surprise we hadn’t planned for.
Managing Weight Without Compromise
To reduce the weight, we engineered a core using a MDF + LDF + MDF sandwich structure, replacing 50% of the internal volume with LDF (400 kg/m³) instead of standard MDF (700 kg/m³). The concept worked—until it didn’t.
Due to the project’s design, the edge veneer had to be applied vertically (grain running from bottom to top), unlike the usual horizontal method. This meant we had to edge-band before veneering the surface, reversing the standard process.
The result? While the edges looked beautiful, the pressing force used to apply the veneer began deforming the softer LDF inside, creating unwanted bubbles and fracture lines—and irreparably damaging several tabletops.
The Solution: Precision Calibration
After significant testing, we managed to recalibrate the press to apply just enough pressure to achieve strong adhesion to the MDF layers—without compromising the softer LDF in the middle.
The result: after many iterations, rework, and investment, we successfully developed a solid, elegant and technically refined coffee table with Burl veneer and 65 mm thickness. They’re bold. They’re beautiful. And they now grace some of the most tasteful interiors around the world.
Final Thought
This story isn’t about cost overruns. It’s about problem-solving, craftsmanship, and the kind of real-world challenges that make a good manufacturer into a great partner. At Flexhouse, we don’t shy away from complex ideas—we lean in and figure them out.