Arbeiten mit Burl: Wenn Schönheit auf Komplexität trifft
Bei Flexhouse scheuen wir keine mutigen Designherausforderungen. Kürzlich hatten wir die Gelegenheit, ein Projekt für eine renommierte globale Marke umzusetzen, das eines der faszinierendsten Materialien in der Holzbearbeitung betraf: Burl-Furnier, speziell Burl-Eiche und Burl-Walnuss (Amerikanische Schwarznuss).
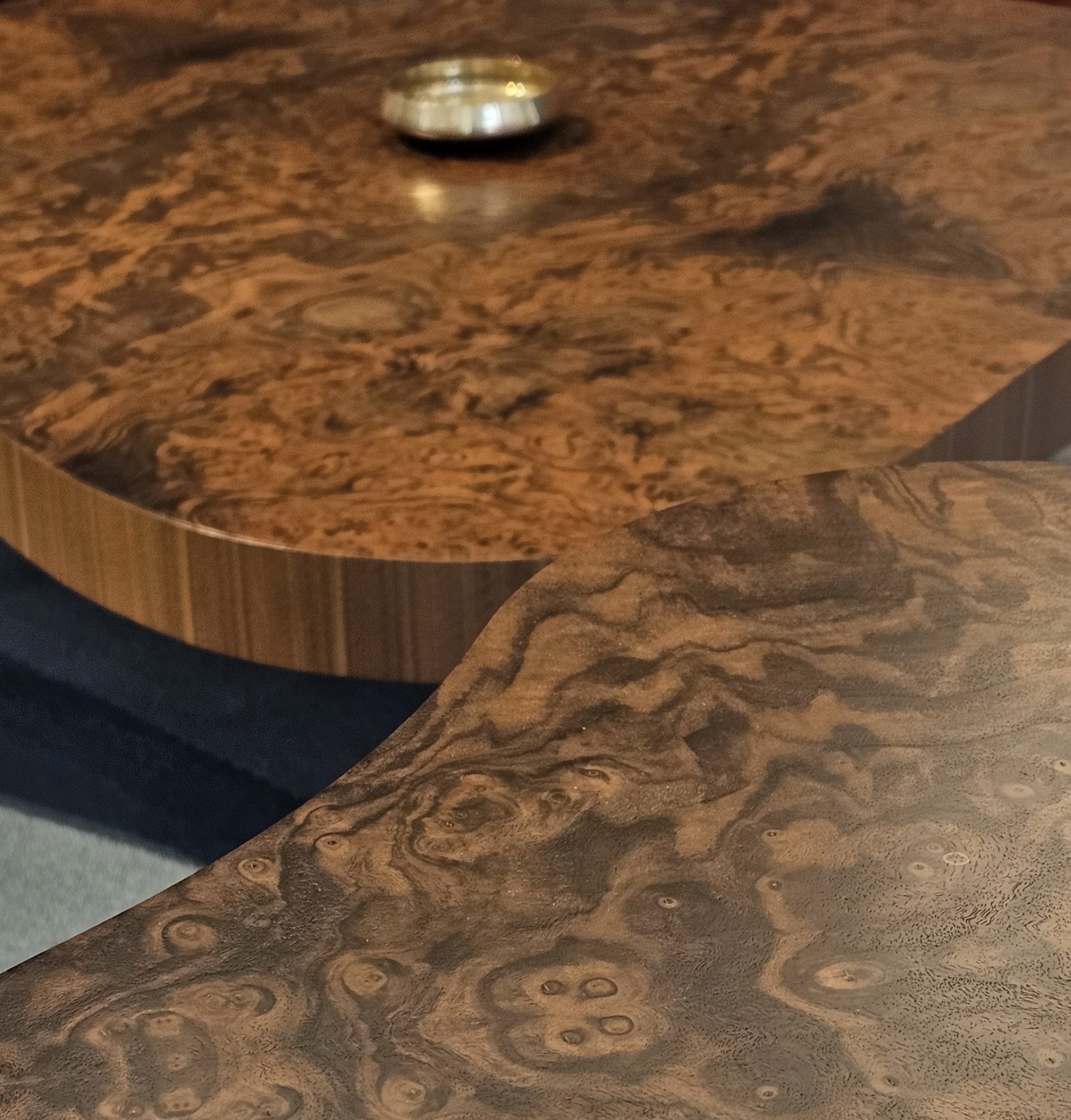
Zunächst waren wir begeistert von der Tiefe des Designs und den Lernmöglichkeiten. Doch im Verlauf des Projekts erkannten wir schnell, wie viele Produktionsherausforderungen dieses schöne, aber launische Material mit sich bringen würde.
Selten, roh & unnachgiebig: Die Natur des Burl
Burl-Furnier ist bekannt für seine intensiv gemaserte Struktur, die eine visuelle Tiefe erzeugt, die von geradlinigen Hölzern nicht nachgebildet werden kann. Doch diese Schönheit hat ihren Preis: Um nur einen Quadratmeter einer Tischoberfläche zu bedecken, mussten wir bis zu acht einzelne Furnierblätter mit jeweils einzigartigem Muster zusammenfügen.
Hochwertiges Burl-Furnier zu finden, ist eine Herausforderung für sich. Es ist selten, kommt oft in kurzen oder schmalen Blättern und viele davon weisen Risse, Hohlräume oder Wurmlöcher auf. Um diese Probleme zu lösen, entwickelten wir eine spezielle Wachstechnik, um das Material zu versiegeln und zu stabilisieren, bevor der Veredelungsprozess begann.
Von Handarbeit zu Innovation: Die 65-mm-Herausforderung
Das Design verlangte eine Tischplatte mit einer Stärke von 65 mm – eine Seltenheit bei Furnierarbeiten. Keine Maschine auf dem Markt konnte Kantenbänder bei dieser Dicke anbringen, also mussten wir es zunächst von Hand machen. Möglich, aber langsam und wenig präzise.
Schließlich arbeiteten wir mit einem dänischen Hersteller zusammen, um eine maßgeschneiderte Kantenanleimmaschine zu entwickeln, die 65 mm bewältigen konnte. Dies brachte Präzision und Geschwindigkeit – offenbarte jedoch auch ein neues Problem: Die größere Version des Tisches wurde so schwer, dass vier Personen nötig waren, um ihn von der Lackierstraße zu heben – eine logistische Überraschung, mit der wir nicht gerechnet hatten.
Gewicht managen ohne Kompromisse
Um das Gewicht zu reduzieren, entwickelten wir einen Kern aus einer MDF + LDF + MDF-Sandwichstruktur und ersetzten 50 % des Innenvolumens durch LDF (400 kg/m³) anstelle von Standard-MDF (700 kg/m³). Das Konzept funktionierte – zunächst.
Aufgrund des Designs musste das Kantenfurnier vertikal (von unten nach oben) angebracht werden, im Gegensatz zur üblichen horizontalen Methode. Das bedeutete, dass wir die Kante vor der Furnierung der Oberfläche anbringen mussten – ein umgekehrter Standardprozess.
Das Ergebnis? Während die Kanten wunderschön aussahen, führte die beim Verpressen eingesetzte Kraft dazu, dass das weichere LDF im Inneren deformiert wurde – es entstanden unerwünschte Blasen und Bruchlinien, wodurch mehrere Tischplatten irreparabel beschädigt wurden.
Die Lösung: Präzise Kalibrierung
Nach umfangreichen Tests gelang es uns, die Presse so neu zu kalibrieren, dass gerade genug Druck ausgeübt wurde, um eine starke Haftung an den MDF-Schichten zu erreichen – ohne das weichere LDF im Inneren zu beschädigen.
Das Ergebnis: Nach vielen Iterationen, Nacharbeiten und Investitionen entwickelten wir erfolgreich einen soliden, eleganten und technisch raffinierten Couchtisch aus Burl-Furnier mit 65 mm Stärke. Sie sind mutig. Sie sind schön. Und sie zieren heute einige der stilvollsten Innenräume der Welt.
Abschließender Gedanke
Diese Geschichte handelt nicht von Kostenüberschreitungen. Es geht um Problemlösungen, Handwerkskunst und die Art von Herausforderungen aus der Praxis, die einen guten Hersteller zu einem großartigen Partner machen. Bei Flexhouse scheuen wir uns nicht vor komplexen Ideen – wir nehmen sie an und finden Lösungen.