Bei Flexhouse gehen wir gerne aus unserer Komfortzone heraus, und unser erster Vorstoß in Betonmöbelkomponenten hat das gerade bewiesen.
Als wir die Entwicklung großer Betonbeine für einen Tisch mit Glasplatte aufnahmen, betraten wir Neuland. Es folgte eine Reise aus Versuchen, Fehlern, Neugestaltungen und Durchbrüchen, die in einer Lösung gipfelten, auf die wir stolz sind.
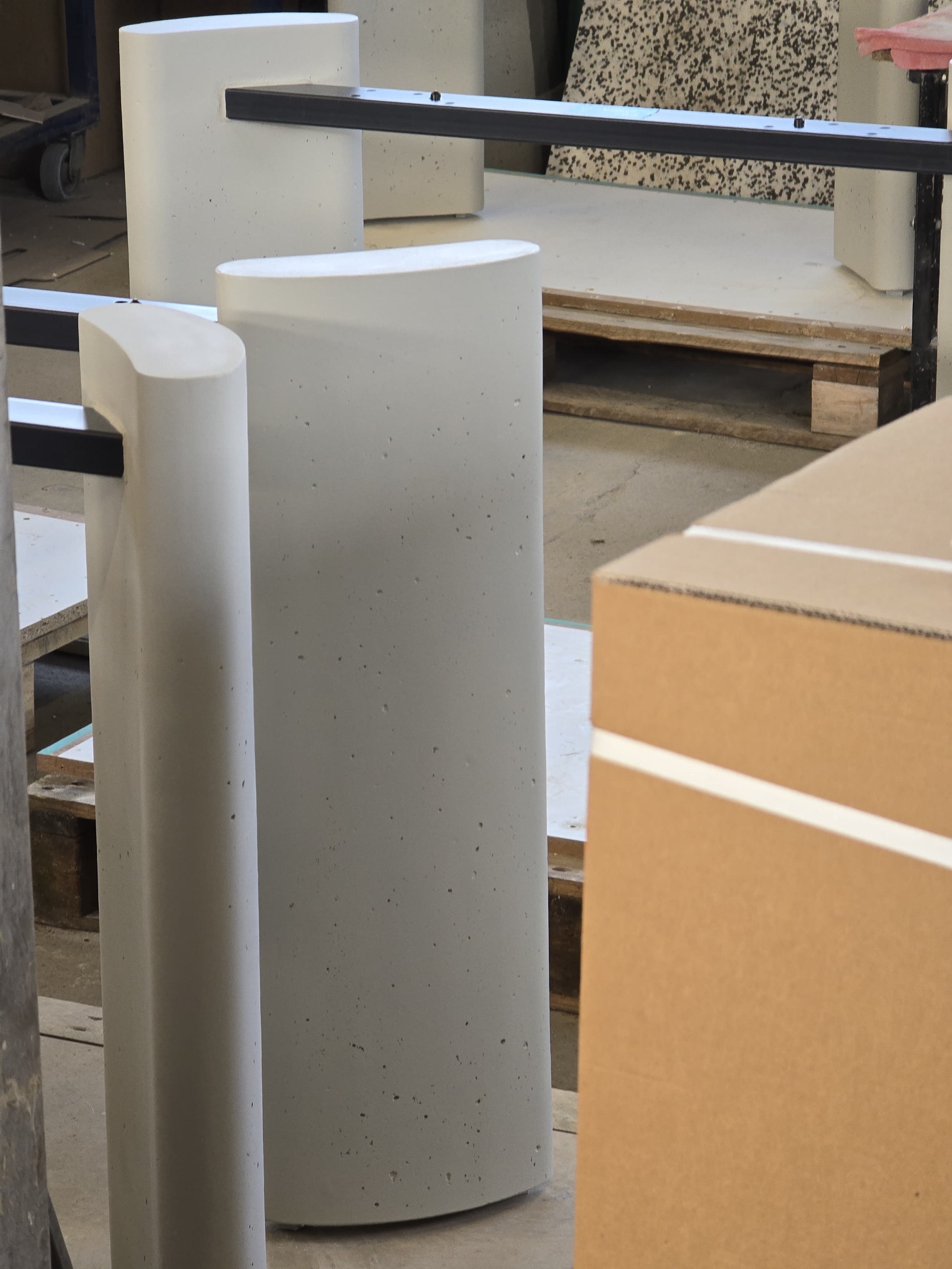
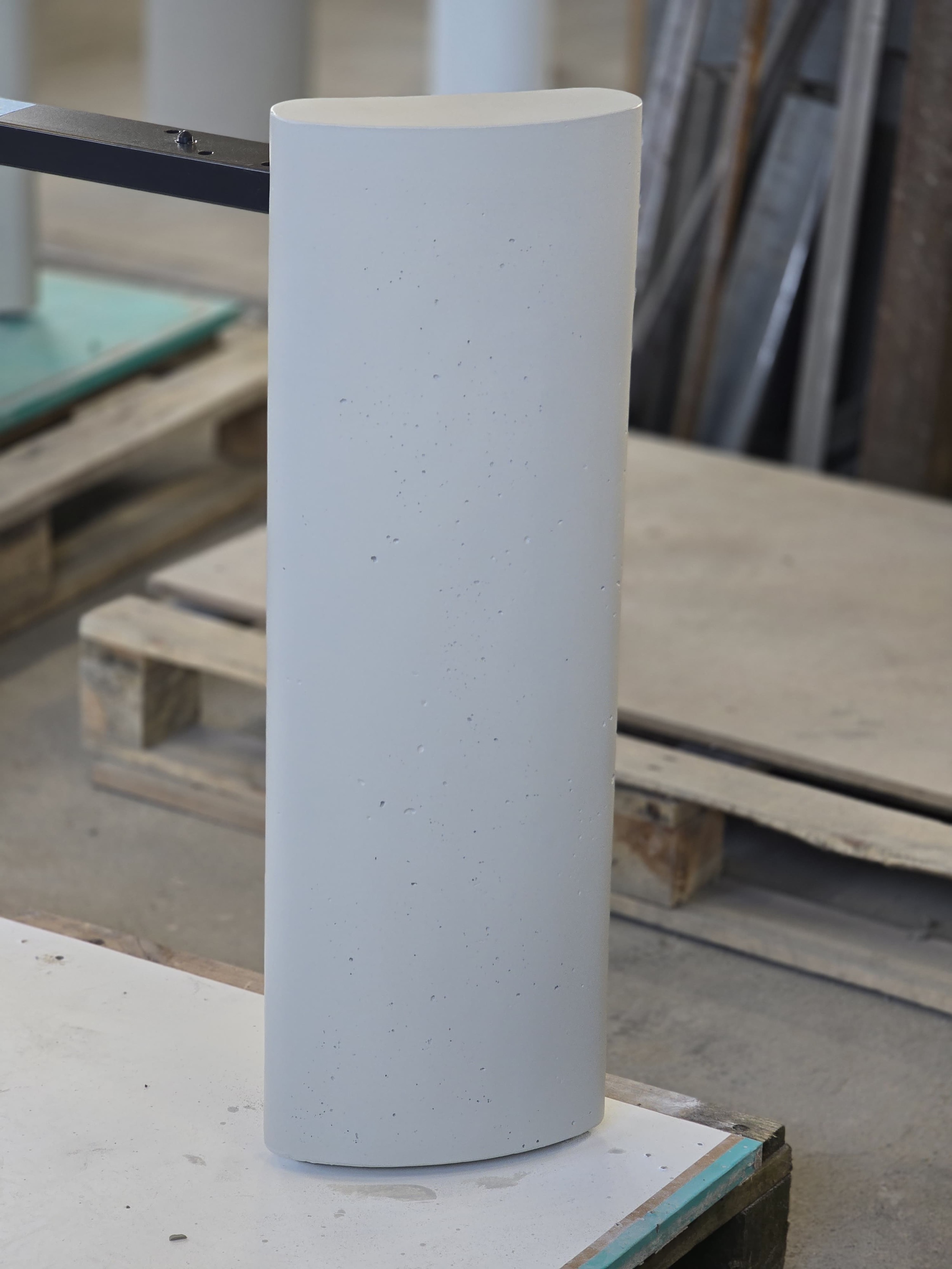
Die Herausforderung: Beton trifft auf Stahl
Das anfängliche Briefing war ehrgeizig: in Beton gegossene Beine mit schlanker Silhouette, kombiniert mit einem Stahleinsatz für interne Unterstützung und Stabilität. Obwohl das Design auf Papier beeindruckend aussah, offenbarte es schnell seine Achillesferse beim Testen: Risse.
Warum? Beton schrumpft natürlich, wenn er trocknet. In Kombination mit einem starren internen Stahlrahmen und einer dünnen Betonschale (nur 15 mm) führte die Spannung zu sichtbaren Rissen, manchmal in mehrere Richtungen. Zwei unserer ersten Beine rissen irreparabel, bevor sie sogar die Fabrik verließen.
Die Lernkurve: Lösungen erforschen
- Gummibeschichtung: Das Aufsprühen einer Gummischicht auf den Stahlrahmen war unsere erste Idee. Leider war diese Methode zu zeitaufwendig, umweltbedenklich und schwer in der Produktion zu kontrollieren.
- Chemisches Additiv LBN: Wir integrierten ein ungiftiges Betonzusatzmittel (LBN), eine wässrige Lösung von oberflächenaktiven Stoffen. Obwohl sicher (nicht gefährlich nach EU-Verordnung, ohne PFAS oder Formaldehyd), verbesserte es die Elastizität nur geringfügig.
-
Überarbeitetes Aushärteprotokoll: Wir führten einen mehrstufigen Trocknungsprozess ein:
- 3 Tage Einweichen
- 2 Tage natürliche Trocknung
- 1 Tag Nachhärtung. Dies stabilisierte das Schrumpfen, aber die Rissbildung war immer noch inkonsistent.
Der Durchbruch: Schaumstoffband + optimierter Beton
-
PE-Schaumstoffband:
- Ein physikalisch vernetztes Polyolefinschaumband (geschlossenzellige Struktur, silikonbehandelt) wurde direkt auf den Stahlrahmen aufgetragen. Es schuf eine flexible Pufferzone zwischen Stahl und Beton, die Mikrobewegungen während des Aushärtens ermöglichte.
- Chemisch inert, recycelbar und den US-Vorschriften entsprechend
- Ohne Schwermetalle, Formaldehyd oder ozonschädigende Substanzen
-
Modifizierte Betonmischung:
- Wir entwickelten eine neue Formel, angereichert mit Glasfasern und alternativen Zementarten, die die Brüchigkeit reduzierte, während das gewünschte ästhetische Erscheinungsbild beibehalten wurde.
-
Werkzeugpräzision:
- Die Schaumschicht wurde als schnellklebender Streifen aufgetragen (anstatt gesprüht), was Zeit sparte und die Reproduzierbarkeit verbesserte.
Ergebnisse: Stabilität erreicht
Nachdem wir die Änderungen umgesetzt hatten, fertigten wir acht neue Beinprototypen. Alle wurden mit dem überarbeiteten Prozess ausgehärtet. Nach einer Überwachungszeit von 3-4 Wochen zeigte keiner von ihnen die Rissprobleme des ursprünglichen Batches. Selbst unter ISTA-Simulationsbedingungen blieben die Beine stabil und strukturell intakt. Das Produkt wird in den kommenden Monaten auf den Markt kommen.
Abschließende Gedanken
Wir teilen diese Erfahrung nicht nur als Fallstudie, sondern als Einladung: Wenn Sie an Betonmöbeln arbeiten und ähnliche Herausforderungen bewältigen, hoffen wir, dass unsere Erkenntnisse Ihnen von Nutzen sind. Und wenn Sie einen Produktionspartner suchen, der nicht davor zurückschreckt, neue Materialien zu erkunden, würden wir gerne von Ihnen hören. Bei Flexhouse glauben wir, dass Innovation oft nicht aus dem Vermeiden von Fehlern, sondern aus ihrer klugen Lösung entsteht.
Lassen Sie uns etwas Großartiges bauen.