At Flexhouse, we love stepping outside our comfort zone—and our first foray into concrete furniture components proved to be just that.
When we took on the development of large concrete legs for a glass-top table, we were entering uncharted material territory. What followed was a journey of trial, failure, redesign, and breakthrough—culminating in a solution we’re proud to share.
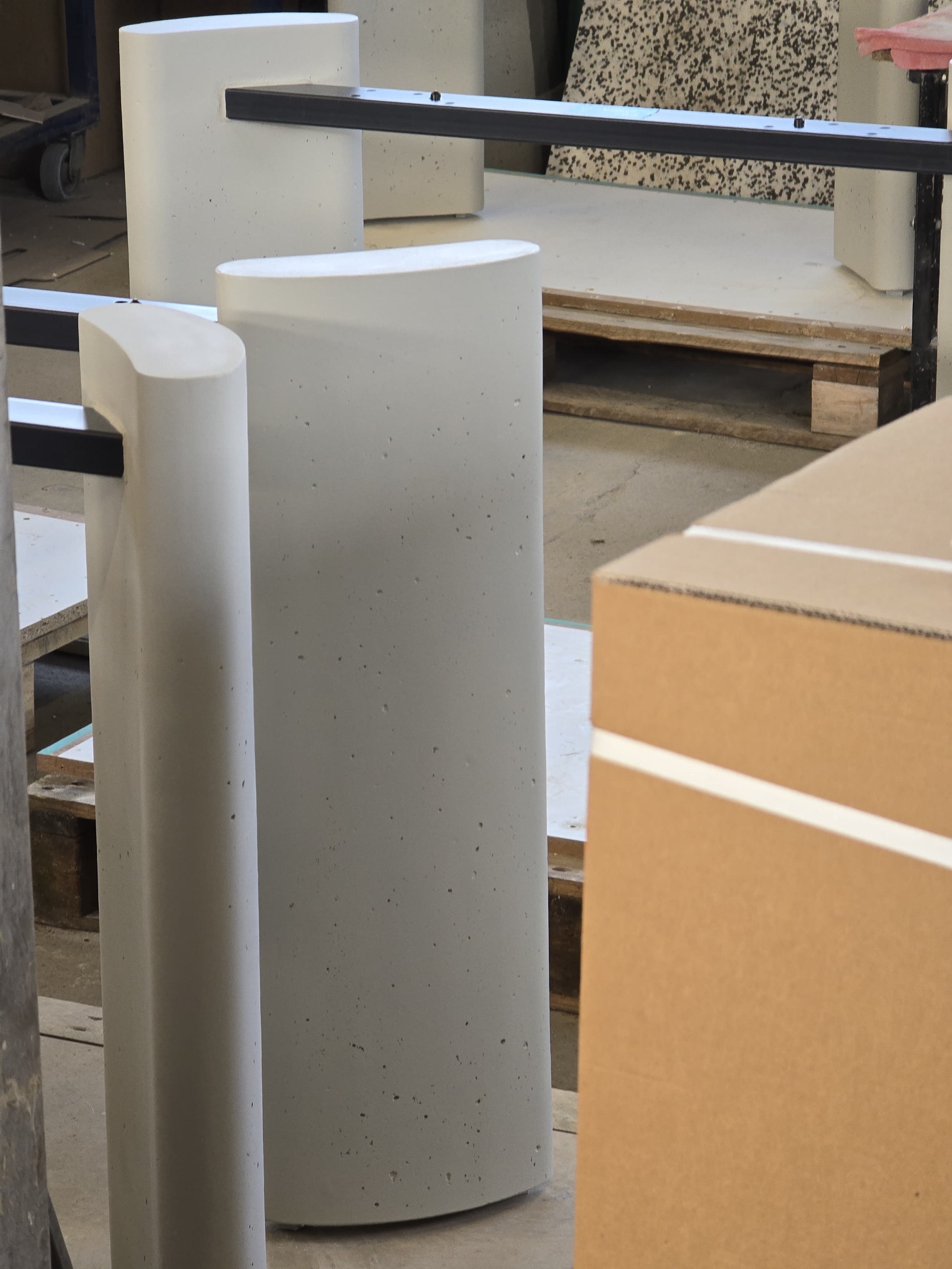
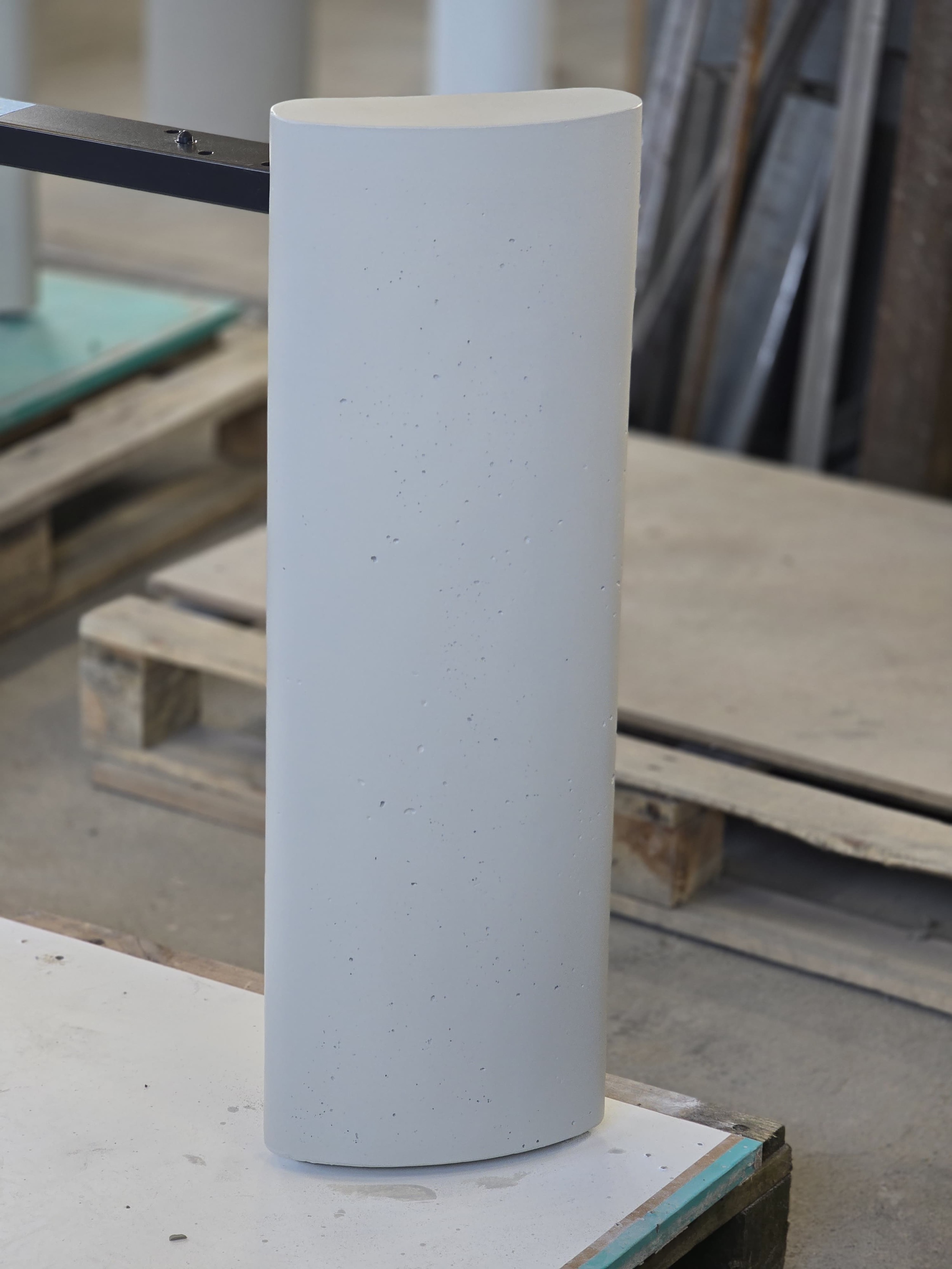
The Challenge: Concrete Meets Steel
The initial brief was ambitious: cast-in-concrete legs with a slim silhouette, paired with a steel insert for internal support and stability. While the design looked stunning on paper, it quickly revealed an Achilles' heel during testing: cracks.
Why? Concrete naturally shrinks as it dries. Combined with a rigid internal steel frame and a thin concrete shell (just 15 mm), the tension caused visible cracking, sometimes in multiple directions. Two of our first legs cracked beyond repair before even leaving the factory.
The Learning Curve: Exploring Solutions
- Rubber Layer Coating: Spraying a rubber layer onto the steel frame was our first idea. Unfortunately, this method was too time-consuming, environmentally sensitive, and difficult to control in production.
- Chemical Additive LBN: We integrated a non-toxic concrete additive (LBN), a water-based solution of surface-active agents. While safe (non-hazardous under EU regulation, no PFAS or formaldehyde), it only slightly improved elasticity.
-
Revised Curing Protocol: We introduced a multi-stage drying process:
- 3 days of soaking
- 2 days of natural drying
- 1 day of post-cure heating This stabilized the shrinkage, but cracking was still inconsistent.
The Breakthrough: Foam Tape + Optimized Concrete
-
PE Foam Tape:
- A physically cross-linked polyolefin foam tape (closed-cell structure, silicone-treated) was applied directly to the steel frame. It created a flexible buffer zone between the steel and concrete, allowing micro-movements during curing.
- Chemically inert, recyclable, and compliant with U.S. regulations
- No heavy metals, formaldehyde, or ozone-depleting substances
-
Modified Concrete Mix:
- We developed a new formula enriched with glass fibers and alternative cement grades, reducing brittleness while maintaining the desired aesthetic.
-
Tooling Precision:
- The foam layer was applied as a quick-glue strip (instead of sprayed), saving time and enhancing reproducibility.
Results: Stability Achieved
After implementing the changes, we completed eight new leg prototypes. All were cured using the revised process. After a monitoring period of 3–4 weeks, none of them exhibited the cracking issues of the original batch. Even under ISTA simulation conditions, the legs remained stable and structurally sound. The product is expected to launch in the coming months.
Final Thoughts
We’re sharing this experience not just as a case study, but as an invitation: If you’re working on concrete-based furniture and facing similar challenges, we hope our learnings are valuable to you. And if you're looking for a production partner unafraid to dive into new materials, we’d love to hear from you. At Flexhouse, we believe innovation often comes not from avoiding mistakes—but from solving them smartly.
Let’s build something great.